Welcome to our comprehensive guide on concrete pricing per cubic meter (m3) in New Zealand. Whether you’re planning a home renovation, building a new driveway, or tackling a larger construction project, understanding the costs involved in sourcing and laying concrete is essential. In this article, we’ll break down the key factors that affect concrete prices, provide up-to-date cost estimates for 2025, and offer practical tips for managing your budget. From material and transportation fees to labor and potential add-ons, we’ll help you get a clearer picture of what to expect and how to make informed decisions for your next project.
The concrete price per m3 in NZ typically ranges from NZD $160 to $250 in 2025, depending on factors such as location, type of concrete mix, and delivery requirements. Urban areas generally have lower prices due to easier access to suppliers, while rural locations may face higher costs due to transportation. Specialty mixes like colored or reinforced concrete can also increase the price. To get an accurate estimate, consider additional costs like delivery fees, site preparation, and labor.
- What Factors Affect Concrete Prices In New Zealand
- Average Concrete Price Per M3 In NZ (2025 Estimates)
- Additional Costs To Consider In Your Concrete Project
- Cost-Saving Tips For Your Concrete Project
- FAQs: About Concrete Price Per M³ NZ
- Why does the price of concrete vary so much in New Zealand?
- What is the average price of concrete per cubic meter (m3) in NZ in 2025?
- How can I calculate the amount of concrete I need for my project?
- Are there any hidden costs when ordering concrete in New Zealand?
- Is it cheaper to mix concrete myself or order pre-mixed concrete?
- where precise consistency is not critical.How does the type of concrete affect the price per cubic meter?
- Why is concrete more expensive in rural areas of New Zealand?
- Can I get a discount if I order concrete in bulk?
- How long does it take for concrete to cure, and does this affect pricing?
- What should I consider when choosing a concrete supplier in NZ?
- Conclusion
What Factors Affect Concrete Prices In New Zealand
When planning a construction project, it’s essential to understand the various factors that influence concrete prices in New Zealand. Whether you’re building a residential driveway, laying a foundation for a commercial structure, or undertaking a large-scale infrastructure project, the cost of concrete can fluctuate based on several key elements. Below, we break down the primary factors that affect concrete pricing in NZ, helping you better estimate your project’s budget.
Raw Material Costs
Concrete is made up of several core ingredients, including cement, aggregates (such as sand and gravel), water, and additives. Each of these components contributes to the overall price of the concrete. Here’s how they affect costs.
- Cement: As the key binding agent, cement plays a significant role in the price of concrete. Cement prices can vary depending on global supply chain issues and production costs.
- Aggregates: The quality and availability of aggregates (gravel, sand, and crushed stone) can impact the final price. High-quality aggregates may be more expensive, and the distance from the source of these materials to your project site will also add to the cost.
- Additives: Special additives, such as those that speed up curing times or enhance durability, can further increase the price. Some projects require high-strength or more durable mixes, which can lead to higher costs.
- Regional Variations: It’s also important to consider where you’re located. Prices for raw materials can be higher in remote regions of New Zealand due to increased transportation and supply chain challenges. For example, concrete projects in rural areas may face higher raw material costs compared to those in urban centers where suppliers are more readily available.
Transportation Costs
One of the major factors influencing the price of concrete is how far it needs to be transported from the batching plant to your construction site. Delivery distances can affect costs in a few key ways.
- Proximity to Supplier: If your site is located far from a ready-mix concrete plant, expect to pay more in transportation fees. This is especially true for rural or isolated areas where fewer concrete suppliers operate.
- Fuel Costs: Rising fuel prices can also increase the cost of delivery. A spike in fuel costs can make long-distance deliveries significantly more expensive, directly affecting your project’s budget.
- Urban vs. Rural Transport Costs: In urban areas like Auckland, Christchurch, or Wellington, transport costs may be lower due to the proximity of suppliers and better infrastructure. However, in more remote or rural areas, where concrete plants are scarce, the cost of delivery can drive up the price per cubic meter (m³).
Labour and Installation
While raw materials and transport are important, labour costs also play a significant role in determining the total price of concrete. The process of preparing, pouring, leveling, and finishing the concrete requires skilled labour, which can be expensive depending on the complexity of the project.
- Site Preparation: The cost to prepare a site for concrete pouring varies depending on factors like terrain, soil type, and whether any demolition or excavation is needed.
- Pouring and Leveling: Proper installation of concrete requires experienced workers to pour, level, and smooth the material. In some cases, additional equipment like concrete pumps or mixers may be needed, increasing labour costs.
- Finishing: Special finishes, such as stamping, polishing, or sealing, will add to the total price. Labour costs may also increase if your project requires more detailed or time-consuming finishing work.
Supply and Demand
Market conditions can have a significant impact on concrete prices in New Zealand. The laws of supply and demand play a critical role, especially during peak construction periods.
- Seasonal Fluctuations: Construction activity typically increases during warmer months, which can drive up the demand for concrete. During these peak periods, suppliers may raise prices due to limited availability.
- Construction Booms: If there is a surge in construction projects, such as during a housing boom or infrastructure development push, the demand for concrete can outstrip supply, further driving up prices.
- Economic Factors: Global economic conditions, changes in the housing market, or government infrastructure spending can all influence the price of concrete. In times of high demand, you might also experience longer lead times and higher costs for rush orders.
Additional Costs
While the base price of concrete includes raw materials and labour, there are often additional costs that can drive up the overall expense of a project. These may include.
- Special Mixes: High-strength or specialized concrete mixes, such as those designed for increased durability or unique conditions, typically come at a higher price.
- Finishes and Treatments: Decorative options, such as colored concrete, stamped designs, or exposed aggregates, can increase costs. Custom finishes not only require additional materials but often take more time to apply, leading to higher labour charges.
- Reinforcements: If your project requires reinforcements, such as steel mesh or rebar, to strengthen the concrete, you can expect to pay extra for both the materials and the labour needed to install them.
Several key factors influence concrete prices in New Zealand, including raw material costs, transportation, labour, supply and demand, and additional project requirements. Understanding these factors can help you better budget for your project and anticipate potential cost variations. Whether you’re working in an urban setting or a remote location, being aware of these variables will allow you to make informed decisions and manage your concrete-related expenses effectively. By considering these elements, you can ensure that your concrete project stays within budget while achieving the quality and durability you need for long-term success.
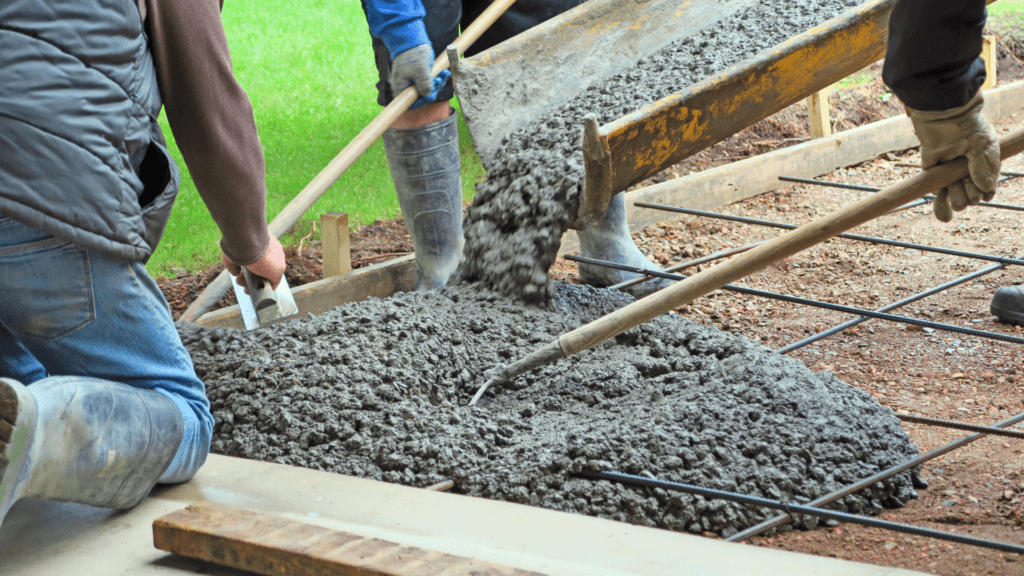
Average Concrete Price Per M3 In NZ (2025 Estimates)
When planning a construction project in New Zealand, one of the key factors to budget for is the cost of concrete, as it is essential to many building processes. Understanding the average price per cubic meter (m3) of concrete helps ensure that projects are cost-effective and stay on track. Below is a detailed breakdown of the estimated concrete costs for 2025, along with factors that influence these prices across different regions and concrete types.
National Average Cost Range for Concrete in 2025
The national average price for concrete in New Zealand varies based on several factors, but for 2025, you can expect prices to range from NZD $160 to $250 per cubic meter (m3). This range is dependent on.
- Location: Urban areas may have higher costs due to demand, while rural areas may face higher prices due to transportation expenses.
- Concrete Grade: Higher-grade concrete, which offers more strength or durability, tends to come at a premium.
- Project Specifics: The complexity of your project, such as whether you’re pouring a simple slab or a foundation requiring reinforced concrete, can influence the final cost.
Concrete Price Breakdown by Region
While the national average gives a rough estimate, concrete prices can fluctuate significantly across different regions in New Zealand. Below are rough estimates for key cities and regions.
- Auckland: In Auckland, the average price per cubic meter of concrete tends to be on the higher end of the scale, ranging from NZD $180 to $250 per m3. The city’s high demand for construction, coupled with transportation logistics in this densely populated urban area, contributes to the increased costs.
- Wellington: The cost in Wellington can range from NZD $170 to $240 per m3. Wellington’s hilly terrain may add to delivery costs, but prices are generally lower than in Auckland due to slightly less demand.
- Christchurch: In Christchurch, expect prices between NZD $160 and $230 per m3. Since the city has been undergoing extensive rebuilding in recent years, the cost of concrete has stabilized somewhat, though ongoing projects still create steady demand.
Urban vs. Rural Differences
Concrete prices can also vary significantly depending on whether you’re in an urban or rural area. Urban areas tend to have slightly higher prices due to increased demand and the ease of access to concrete suppliers. In contrast, rural areas may see a noticeable price increase, often an additional NZD $20 to $40 per m3 due to the cost of transporting the concrete over longer distances. Limited supplier options in remote regions can also play a role in driving prices up.
Price for Different Types of Concrete
Concrete comes in various forms, each suited to different types of construction projects. The type of concrete you choose will significantly impact the cost per cubic meter.
Standard Concrete
For most standard construction projects, regular concrete will suffice. Standard concrete is typically used for general slabs, driveways, and basic foundations. The cost for standard-grade concrete generally falls within the NZD $160 to $200 per m3 range, depending on your location and project specifications.
Specialty Concrete
There are several types of specialty concrete, each designed for specific uses. These types often come at a higher cost due to the added materials or labor involved in their production.
- Colored Concrete: Adding color to concrete can increase the aesthetic appeal, particularly for driveways, patios, or interior flooring. Colored concrete usually costs NZD $220 to $300 per m3, depending on the color and finish.
- Polished Concrete: Polished concrete is popular for its sleek, modern look. Often used in interior spaces like commercial buildings or high-end homes, the cost for polished concrete can range from NZD $250 to $350 per m3, depending on the level of polish and the size of the area.
- Reinforced Concrete: Reinforced concrete, which includes steel or other materials to increase strength, is often required for structural foundations or multi-story buildings. The addition of reinforcing materials adds to the price, typically increasing the cost to NZD $220 to $280 per m3.
When is Specialty Concrete Necessary
Specialty concrete is often used when specific performance characteristics are required for the project. For example.
- Colored concrete: might be chosen for its aesthetic value in a visible area such as a patio.
- Reinforced concrete: is essential for projects that require extra strength, such as high-rise buildings or large structural supports.
- Polished concrete: is ideal for modern commercial or residential spaces that seek a smooth, durable finish.
While these specialty options provide clear advantages, they also increase the overall cost of the project. It’s important to weigh the benefits against the added expense when planning your construction budget. In 2025, the cost of concrete in New Zealand will continue to vary depending on factors like location, concrete grade, and project requirements. Whether you are working on a small home improvement project or a large-scale commercial build, understanding the cost per cubic meter for different types of concrete and in various regions will help you manage your budget effectively. For an accurate estimate, always consider consulting with local suppliers, as they can provide region-specific pricing and offer advice on the best concrete type for your needs.
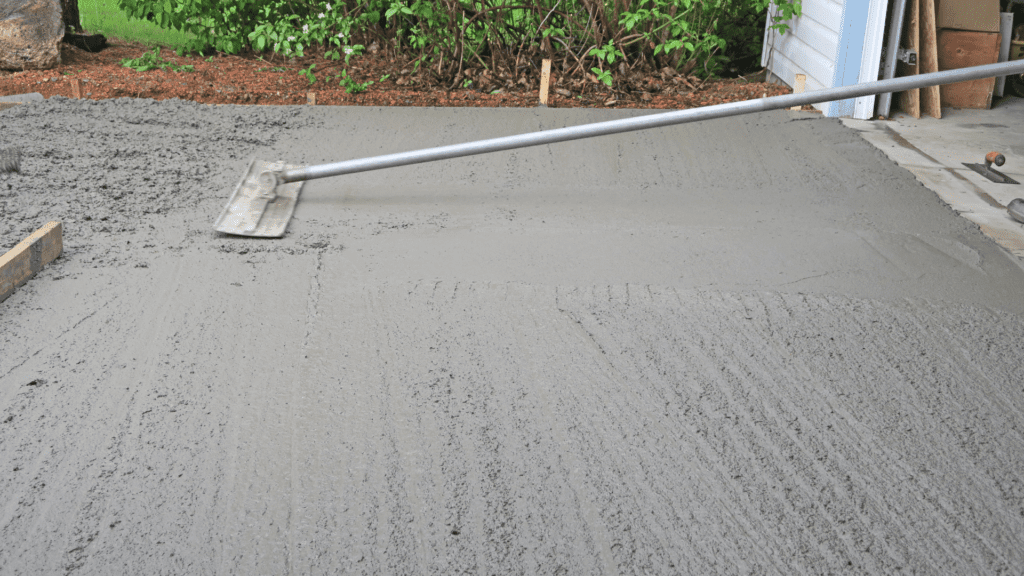
Additional Costs To Consider In Your Concrete Project
When planning a concrete project, it’s easy to focus solely on the cost of the concrete itself. However, many homeowners and builders overlook additional expenses that can significantly impact the final budget. To avoid unpleasant surprises, it’s essential to understand these hidden costs upfront. Below, we’ll explore some key factors that can influence your concrete project’s overall price.
Site Preparation
Before any concrete is poured, your site must be properly prepared. Often, excavation, soil removal, and base layer preparation are not included in the initial concrete pricing. These preparatory tasks are essential to ensuring that the concrete has a stable foundation. For example, if your site is sloped or has existing structures that need removal, it will require more labor and equipment, thus increasing your overall expenses.
The cost of site preparation can vary significantly depending on the condition of your land. A flat, clear site will naturally be less expensive to prepare compared to one that requires heavy excavation. Additionally, soil types may require special treatment, and the need to bring in a gravel base or compact the soil can add further costs. Factoring in these potential expenses early in your budgeting process can help avoid unexpected spikes in the project’s total cost.
Reinforcements and Additives
Concrete is strong, but when it comes to building projects such as driveways, foundations, or slabs, reinforcements like steel mesh or rebar are often needed to improve durability and structural integrity. Adding these materials will raise the price per cubic meter (m3) of concrete used in your project. Reinforcements are especially important in areas with high traffic or where the concrete will need to support heavy loads, such as in industrial projects or large residential builds.
Additionally, certain projects may require chemical additives to ensure the concrete performs well under specific conditions. For instance, if your project is happening in colder weather, you might need accelerants to speed up the curing process. While these additives are crucial for maintaining the quality and longevity of your concrete, they do come at an extra cost. These seemingly small additions can significantly influence your overall budget.
Delivery and Pumping Costs
The cost of delivering concrete to your site is another factor that can add to your final bill. Depending on how far your project is from the concrete supplier, delivery fees can vary greatly. For projects located in remote areas or those that require a significant amount of concrete, these costs can become substantial.
Access to your site is another element that affects delivery costs. If your project is in a hard-to-reach location, you may need to hire a concrete pump truck to get the material to the required area. Pump trucks are often used when the site is not accessible by standard delivery trucks, such as in areas with limited space or where obstacles like fences or buildings are present. While necessary in many cases, the use of pump trucks adds an additional fee to the overall project cost, which should be considered during the planning phase. While concrete itself may seem affordable, the associated costs can quickly add up. Site preparation, reinforcements, and delivery logistics are all factors that can significantly increase the final bill. Properly accounting for these additional expenses in your initial budget will help ensure your concrete project stays on track and avoids costly surprises.
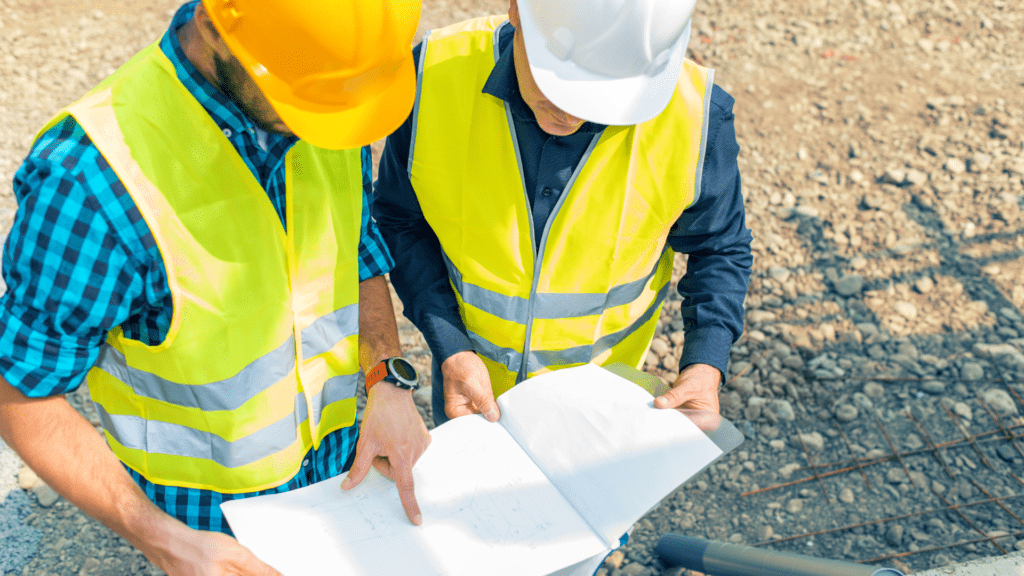
Cost-Saving Tips For Your Concrete Project
Undertaking a concrete project can be a significant investment, but with the right approach, you can maximize value without sacrificing quality. Whether you’re planning a small patio, driveway, or foundation, these cost-saving strategies will help you make the most out of your concrete project.
Order the Right Amount of Concrete
One of the easiest ways to overspend on a concrete project is by ordering the wrong amount of concrete. Both under-ordering and over-ordering can lead to unnecessary expenses.
When you order too much concrete, you’re paying for material you won’t use. On the other hand, under-ordering means you’ll need to place another order, often incurring additional delivery fees and wasting valuable time. To avoid this, calculate the volume of concrete you need accurately.
How to calculate concrete volume
- Measure the length, width, and depth of your project area.
- Multiply these dimensions to get the total cubic feet (or meters) of the space.
- Convert to cubic yards or cubic meters (since concrete suppliers typically sell by the yard or meter) by dividing by 27 (for yards) or adjusting based on the metric system.
For example, if you’re working on a driveway that’s 20 feet long, 10 feet wide, and 4 inches deep, you’d calculate it as follows.
- Length (20 ft) x Width (10 ft) x Depth (0.33 ft) = 66 cubic feet.
- 66 cubic feet ÷ 27 = 2.44 cubic yards of concrete.
By ensuring accurate calculations, you’ll avoid wasted materials and reduce costs.
Plan for Multiple Uses in One Delivery
If you have several small concrete projects, such as a patio, garden walkway, and fence post footings, try to group them into one delivery. This can help save money on transportation costs, which can add up quickly if you’re paying for multiple deliveries.
Batching smaller projects into one concrete order also allows you to get a bulk price, which may be lower than if you were to order each one separately. Be sure to have all your prep work done ahead of time so that the concrete can be poured without delays, avoiding the risk of it hardening prematurely.
Compare Suppliers
The cost of concrete can vary significantly depending on the supplier. Shopping around and comparing quotes from local concrete suppliers can make a big difference in your overall project cost. Look for suppliers that offer competitive pricing without compromising on quality.
When evaluating suppliers
- Get multiple quotes: To ensure you’re getting the best deal.
- Check reputations: By reading online reviews and asking for recommendations from friends or neighbors who have completed similar projects.
- Consider local suppliers:Who may offer lower transportation costs and faster delivery times, both of which can save you money and time.
Never settle for the first price you receive spending a little extra time researching can lead to substantial savings.
Timing Your Project
Did you know that the time of year can impact concrete prices? Concrete suppliers often have busy and slow seasons. Planning your project during off-peak times, such as late fall or early winter, can sometimes result in better pricing.
Demand for concrete is typically lower during these periods, meaning suppliers may offer discounts to keep their business going. Additionally, scheduling your project during less busy times ensures you’re not competing for contractor availability, which can also drive up labor costs.
- Avoid premium charges: If your project isn’t urgent, plan ahead and avoid last-minute orders, which can come with premium delivery fees. By being flexible with your timeline, you can avoid these unnecessary costs.
DIY or Hire a Pro?
Deciding whether to handle a concrete project yourself or hire a professional can significantly impact the overall cost.
DIY Pros
- You save on labor costs.
- It’s a rewarding experience for those who enjoy hands-on work.
DIY Cons
- You may need to rent or purchase tools, which adds to the cost.
- Mistakes can lead to higher expenses in the long run, especially if you need to redo parts of the project.
For smaller, simple projects, such as a small garden path or patio, mixing and pouring the concrete yourself might be a good way to save money. However, for larger or more complex projects like a driveway, foundation, or multi-level structure, it’s often more cost-effective to hire a professional.
Hiring a contractor ensures the job is done correctly and on time, minimizing costly mistakes. Contractors have access to the necessary tools and expertise to handle any challenges that arise, reducing the likelihood of delays or additional expenses due to errors.
When to hire a pro
- If your project involves structural elements, such as a foundation.
- When precise grading and finishing are required.
- If the project area is particularly large or complex.
While hiring a pro may seem more expensive upfront, it can save you money in the long run by avoiding costly errors and ensuring the project is done right the first time. Saving money on a concrete project is all about planning and making informed decisions. By ordering the right amount of concrete, batching multiple projects into one delivery, comparing suppliers, timing your project wisely, and deciding whether to DIY or hire a pro, you can keep your costs under control without sacrificing quality. With these tips, your concrete project can be both successful and budget-friendly.
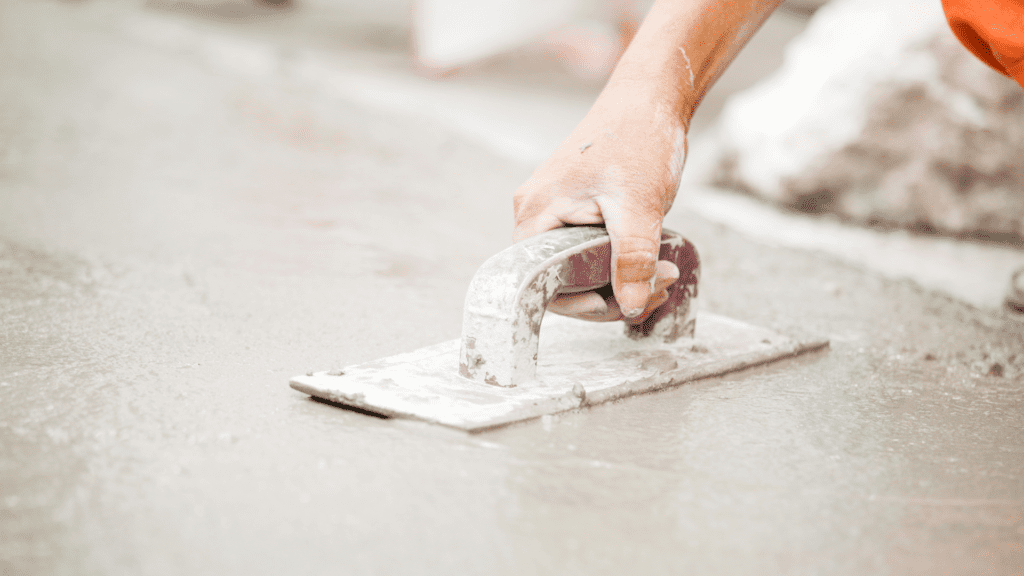
FAQs: About Concrete Price Per M³ NZ
Why does the price of concrete vary so much in New Zealand?
Concrete pricing can vary due to several factors including location, transportation costs, the type of concrete mix required, and local supplier pricing. In rural areas, prices are often higher due to the cost of transporting materials over longer distances. Additionally, specialty mixes like colored or reinforced concrete may also increase the price.
What is the average price of concrete per cubic meter (m3) in NZ in 2025?
On average, the price of concrete per m3 in New Zealand ranges from NZD $160 to $250 in 2025. The price depends on factors such as the specific type of concrete, the volume required, and the delivery location. Urban areas tend to have slightly lower prices compared to rural regions due to easier access to suppliers.
How can I calculate the amount of concrete I need for my project?
To calculate the volume of concrete required, multiply the length, width, and depth of the area in meters (L x W x H). This will give you the volume in cubic meters (m3). For example, for a driveway that’s 10 meters long, 3 meters wide, and 0.1 meters deep, you’d need 3 cubic meters of concrete (10 x 3 x 0.1 = 3 m3).
Are there any hidden costs when ordering concrete in New Zealand?
Yes, there can be additional costs beyond the price of concrete per m3. These can include delivery fees (especially for long distances or hard-to-reach locations), pumping charges if a pump truck is required, and costs for site preparation, such as excavation or leveling. Be sure to ask suppliers for a full breakdown of costs before placing your order.
Is it cheaper to mix concrete myself or order pre-mixed concrete?
For small projects, using pre-mixed bags of concrete might seem more convenient, but for larger projects, ordering ready-mix concrete is typically more cost-effective. Ready-mix concrete saves time and ensures a consistent mix, which is essential for structural integrity. However, DIY mixing might be a good option for very small jobs where precise consistency is not critical.
where precise consistency is not critical.
How does the type of concrete affect the price per cubic meter?
Different types of concrete come at different price points. Standard concrete is less expensive, while specialty mixes, such as high-strength, colored, or polished concrete, tend to cost more. The specific use case and required durability of the concrete will determine which type is necessary for your project, which impacts the final co
Why is concrete more expensive in rural areas of New Zealand?
In rural areas, concrete tends to be more expensive due to higher transportation costs. Since concrete must be delivered in a liquid state, delivery trucks can only travel a limited distance before the concrete begins to set. This limitation increases costs for rural deliveries, especially if the supplier is far from the project site.
Can I get a discount if I order concrete in bulk?
Yes, many suppliers offer discounts for bulk orders. However, this only applies if you can correctly estimate the amount of concrete needed and avoid over-ordering. When placing bulk orders, make sure you have a precise calculation of your requirements to avoid paying for excess material that goes unused.
How long does it take for concrete to cure, and does this affect pricing?
Concrete typically takes about 24-48 hours to set enough for light foot traffic and up to 28 days to fully cure. While curing time itself doesn’t directly affect pricing, certain additives that accelerate or slow down the curing process can increase costs. For example, if you need concrete to cure faster in cold weather, accelerants may be added, which can increase the price per m3.
What should I consider when choosing a concrete supplier in NZ?
When choosing a supplier, consider factors such as reputation, proximity to your project site (to reduce delivery costs), and whether they offer any guarantees or warranties. It’s also important to compare quotes from multiple suppliers to ensure you’re getting a competitive price. Ask about delivery times, extra fees, and whether the supplier offers specialty mixes if needed for your project.
Conclusion
When considering the cost of concrete per cubic meter in New Zealand, several key factors come into play that can significantly impact the final price. Elements such as the type and grade of concrete, local supplier rates, the size and complexity of your project, and additional factors like transportation or labor costs can all contribute to the overall expense. It’s crucial to plan carefully, keeping these factors in mind while budgeting to ensure you avoid unexpected costs that could disrupt your project. Whether you’re laying a driveway or pouring the foundation for a new home, taking the time to assess your needs and budget accordingly can make all the difference in the success of your construction project. To ensure you get the best value, it’s always a smart move to reach out to local suppliers for customized quotes or consider hiring professionals who can manage the process from start to finish. This personalized approach can help avoid surprises and ensure the project is completed to a high standard. In the end, having a clear understanding of concrete pricing and the factors that affect it will help keep your project on track, within budget, and progressing smoothly.
About the Author:
Mike Veail is a recognized digital marketing expert with over 6 years of experience in helping tradespeople and small businesses thrive online. A former quantity surveyor, Mike combines deep industry knowledge with hands-on expertise in SEO and Google Ads. His marketing strategies are tailored to the specific needs of the trades sector, helping businesses increase visibility and generate more leads through proven, ethical methods.
Mike has successfully partnered with numerous companies, establishing a track record of delivering measurable results. His work has been featured across various platforms that showcase his expertise in lead generation and online marketing for the trades sector.
Learn more about Mike's experience and services at https://theleadguy.online or follow him on social media: